Aerial Optical Gas Imaging Increases Inspection Efficiency and Improves Safety
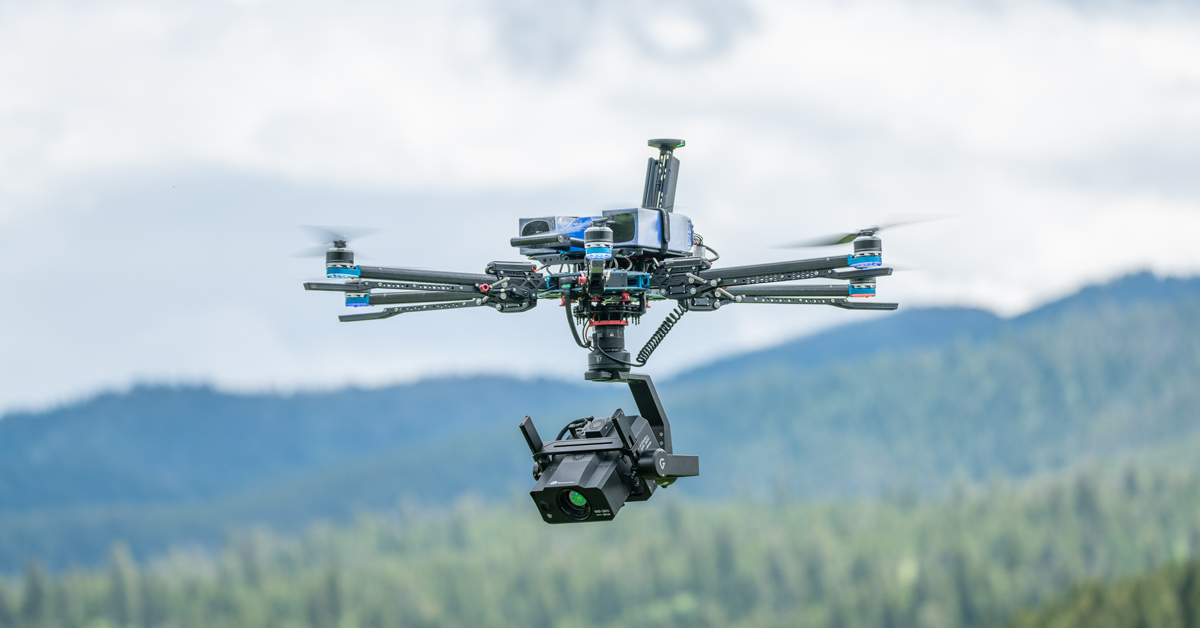
By Steve Beynon – EMEA Optical Gas Imaging Specialist, Teledyne FLIR
Natural gas processing plants, upstream production facilities, compressor stations, and pipelines are critical elements of the natural gas supply chain. These facilities store, process, and transport natural gas through a wide array of equipment over large areas that are difficult to manage efficiently. An important task is finding and limiting—or even eliminating—natural gas leaks from equipment, pipes, and fittings. This not only ensures the safety of employees but also reduces methane emissions that are harmful to the environment. While monitoring gas emissions efficiently across vast gas fields can be challenging, a new, innovative combination of unmanned drones (UAVs) and optical gas imaging technology is proving very useful.
MAKING SAFETY A PRIORITY
Surveying for and repairing natural gas leaks can present a significant health and safety risk for maintenance professionals, despite the many safety measures inspectors and work crews take. Traditional Leak Detection and Repair (LDAR) equipment often requires operators to be close to leaking components or even within the leaking gas cloud. Donning a respirator and other protective equipment takes time and restricts an operator’s ability to move safely. This can all raise the potential for unsafe work practices or injuries while also limiting the capabilities to reach components that may be high off the ground or in hard to access areas. By using optical gas imaging (OGI) cameras to survey for gas leaks, users can spot dangerous leaks from components while working at safe distances; now, with the new aerial solutions in the market, they can get even further away.
Figure 1: Aerial view of a pipeline leak using FLIR OGI technology.
TIME EQUALS MONEY
While handheld OGI cameras resolve many of the safety issues that come with LDAR and increase efficiency, it can still take a lot of time to cover large gas production facilities that don’t provide an easy way to get between the various locations within a system: operators may have to scan an area, drive to the next location, and then start the process over—costing time and money. With new aerial OGI technology, a technician scanning for leaks can cover more facilities or locations in a fraction of the time when compared to handheld operation. An aerial OGI operator can scan 4 or 5 facilities in one flight (depending on a variety of factors), a task that may take half or a full day.
Leaking seal in multiple locations on a floating roof tank identified with a GIS-320
HOW DO YOU GET THERE?
While the facilities in a system or assets within a facility may lookclose on a map, an LDAR professional my find themselves spending considerable time covering a large facility that can span many square kilometers with long distances between assets — making for a very long and inefficient day. For example, an oil and gas operator charged with inspecting a facility with multiple large storage tanks could need an hour or more to check each tank with a handheld OGI camera, as doing so requires climbing the ladder to reach the top of the tank, performing the inspection, then descending the ladder. With an aerial OGI solution, operators can dramatically streamline their processes for LDAR of these tanks by scanning one, after another, after another… all during a single flight. In addition, accessing some sites in the supply chain may be challenging due to location, restrictive land rights, or the sheer size of the area. Using an aerial solution will greatly reduce the time and effort to reach a location that is often challenging, or impossible, without considerable work.
Finally, there is the simple issue of terrain: some pipelines are built in areas that are inaccessible by trucks or even 4-wheelers, creating extreme challenges in inspecting for leaks. Impediments such as rivers, railways, or other obstacles also make aerial OGI more attractive, as you can simply take off from a safe location and quickly reach your site.
Aerial view of a storage tank facility in the oil and gas industry (image courtesy of Zoom Earth). These assets are inspected on a regular basis with OGI to meet regulatory and/or environmental requirements. An aerial OGI solution would allow an operator to inspect multiple assets in one flight.
A BETTER SOLUTION
While there are many drone options on the market, many of these are not dedicated aerial OGI technologies or drones geared for the oil and gas industry. The Workswell GIS-320 aerial OGI solution was built solely for the purpose of gas detection from the sky. Integrated OGI technology from Teledyne FLIR, including the same cooled infrared detector as in the industry-leading FLIR GF320 and GFx320, the GIS-320 was made for the oil and gas industry needs, including U.S. EPA regulatory compliance. With common features like FLIR’s patented High Sensitivity Mode (HSM) image enhancement feature and communications protocol designed specifically for the professional drone operator, the GIS-320 is a valuable addition to an operations LDAR program.
Figure 3: Vision Aerial Vector with GIS-320 OGI payload.
When you pair this payload with an industrial drone platform, oil and gas operators have the most reliable and highest performance aerial OGI solution in the market. Many industrial drone solutions have key features that help aerial OGI inspections such as long flight times, the ability to hot swap batteries, predefined mission plans allowing autonomous inspections, and more. These aerial OGI solutions with a GIS-320 will greatly increase efficiency for companies looking to reduce emissions in their facilities.
GIS-320 from Workswell with Thermal by FLIR
COOLED DETECTOR MAKES THE SMALLEST LEAKS VISIBLE
FLIR OGI cameras can visualize and pinpoint gas leaks that are invisible to the naked eye. Optical gas imaging makes it easy to continuously scan installations that are in remote areas or in zones that are difficult to access. The Workswell GIS-320 with Thermal by FLIR contains a cooled indium antimonide (InSb) detector that produces thermal images of 320 × 240 resolution. With its low F-number (quantitative measure of lens speed) and high sensitivity to gas detection, the GIS-320 detects the smallest of leaks and even meets multiple regulatory sensitivity standards. Switching the camera to HSM further enhances the detection level of the camera so that the smallest gas leaks can be detected. All in all, the GIS-320 with is very easy to control from a safe distance while covering large areas quickly.
Figure 4: Leaking tank on a well pad identified using FLIR OGI technology.
CONCLUSION
Whether you are looking to increase worker safety, meet regulatory requirement or just reduce emissions as better environmental stewards, the applications that require optical gas imaging technology are vast in the oil and gas industry. Many of these are spread out over a small area making it challenging to access easily and quickly. Using a Workswell GIS-320 with Thermal by FLIR and an industrial drone will provide operators with a unique ability to be more efficient in their inspection requirements and more effective in creating safer work environments and reducing emission.